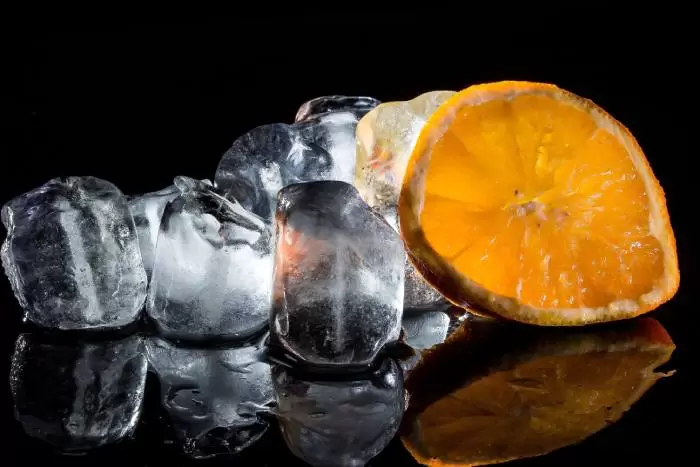
How to Troubleshoot 6 Common Ice Machine Problems
If your restaurant ice machine is down, it can mean big problems for your customers’ experience, and in turn, for your reviews. Try serving room-temperature cocktails at a bar and see how quickly your patrons leave, never to return! And ice machines aren’t just for beverages. They’re also used in hospitals and research facilities for lots of medical and scientific applications.
That’s why it’s so important to get your ice machine up and running as soon as possible. Let’s take a look at some of the most common ice machine problems and how to troubleshoot them.
Insufficient Ice Production
If you’ve noticed a decrease in ice production, several factors could be at play. Start by checking the condenser coil for dirt and debris, as a dirty coil can hinder heat exchange. Verify that the water inlet valve is functioning correctly and providing adequate water flow. Additionally, inspect the evaporator plate for any signs of damage. Regular cleaning, proper water flow, and keeping the machine’s components well-maintained can help restore optimal ice production.
Ice Quality Problems
Cloudy, discolored, or odd-tasting ice can be off-putting to customers or users. Consider checking your water filtration system for clogs or malfunctions, as mineral buildup in the water supply can affect ice quality. Ensure your ice machine is equipped with an effective water filtration system and replace filters regularly to maintain clear and pure ice.
Ice Machine Leaks
Water leaks around your ice machine can be caused by various issues. Inspect the water supply line for any damage and ensure proper connections. A malfunctioning water inlet valve could also be the culprit, leading to overflows and leaks. Regularly inspect and replace worn or damaged components to prevent leaks and potential water damage.
Ice Machine Freezing Up
If your ice machine is producing less ice than usual or the ice is forming irregularly, it might be freezing up. Verify that the defrost timer is functioning correctly, as a malfunctioning timer can lead to excessive ice accumulation. Adequate airflow is crucial to preventing freezing, so ensure the machine is positioned with proper ventilation. Regular defrosting and maintenance can help prevent freezing issues.
Mechanical Failures
Mechanical components such as motors, fans, and sensors can wear out over time, leading to operational disruptions. Regularly inspect these components for signs of wear or malfunction. Ensure that the ice machine is operated within its recommended operating conditions and temperatures. Promptly address any mechanical failures to prevent further damage to the machine.
Scale and Mineral Buildup
Mineral buildup, or scale, can accumulate in ice machines over time due to minerals present in the water supply. Regular descaling is essential to prevent scale buildup in the water lines, evaporator plate, and other internal components. Implement a routine descaling schedule and consider using water treatment systems to reduce mineral content.
Call the Experts
If you’re having difficulty finding the cause of your ice machine problems or if there’s an issue that needs a professional technician, you’re in good hands with K&D Factory Service. We’ve been helping business owners in eastern Pennsylvania with their commercial appliance & equipment needs since 1945, so you can place your trust firmly on our rock-solid reputation! Call 717-236-9039 today to schedule service.